
舟山中遠海運重工持續打造6.36萬噸散貨船精品項目
為持續打造6.36萬噸散貨船精品項目,做精做細做快項目建造,舟山中遠海運重工以“打造精品工程、品牌示范工程”為目標任務,成立63.6k BC項目專項改善委員會,持續優化產品設計、不斷改善建造工藝,生產效率持續加速,建造質量持續增強,客戶滿意度持續提升。
項目建造期間,委員會全體成員廣泛參與,積極發揮作用,圍繞“提升分段制作效率、降低施工難度、縮短船臺搭載周期、提高上水完整性、優化試航流程作業”等方面,重點研究,持續改善,共形成了9大項104小項的改善課題。
經過研討攻關,截至目前已完成67項課題改善,其余課題正在有序推進中。
01.全員參與改善營造良好氛圍
63.6k BC項目專項改善委員會由公司領導牽頭,制造系統各部門/工區負責人、安全/質量/技術負責人、項目經理、總建造師、主管、作業長、工法、工藝等組成,通過廣泛收集結構優化、流程優化、工藝優化、試驗優化、技術優化、科技創新等方面課題,營造了全員參與的良好氛圍。
同時,制造系統定期組織召開分承包方座談會,收集施工人員改善建議,結合現場生產實際,持續改善項目建造過程中的各個環節。
02.優化工藝工法提高生產效率
63.6k BC項目上水前,將原舵葉封固方式進行優化改善,采用工裝對舵桿進行封固,減少了焊接及拆除作業,避免了舵葉及掛舵臂的油漆破損及修補,徹底消除了帶纜艇水上作業,提高了生產安全性。
對63.6k BC項目17個總組/搭載總段快速松鉤工藝進行優化,區分保安全封焊和保精度封焊,單船可減少吊車等待時間52小時,降低人工浪費的同時,提高了吊車使用率。
03.推廣工裝治具降低人工成本
建造項目腳手架搭設需要大量人工,在63.6k BC項目上設計制作軸舵系施工專用平臺代替傳統腳手架,提高了工作效率降低了人工成本。該施工平臺為組合模塊化設計,在船臺上鋪設有軌道,根據施工可以前后移動,工人在平臺上施工安全方便。
同時在10C總段、海水箱、C型總段、甲板總組段等17處設計使用工裝腳手,減小施工難度,一艘船可以節約640余工時。
04.定制化生產提高場地利用率
為提高船臺場地利用率,改善小組根據船臺總組場地尺寸、吊車參數、生產計劃、總段尺寸、總組周期等實際因素,研討策劃采用船臺總組場地定制化生產方式,增加了80A/20B總段及4個克令吊塔身總組場地,總組墩木無需反復擺放,實現系列船永久使用,單船可節約250工時。
10C總段總組位置定制后,外板腳手架實現一次搭設系列船永久使用。橫艙壁總段和C型段定制后反面腳手架和C型總段上下梯子也成功實現定制,一次搭設永久使用,場地利用率大幅提升,人工成本持續降低。
05.優化施工流程縮短建造周期
在63.6k BC項目N1087船上,通過持續優化施工流程,實現發電機船臺搭載階段動車、主機在船臺搭載階段串油,相較于首制船縮短水下周期21天。
針對試航流程進行專項梳理,主機耐久試驗和測速一起,節省試航時間10小時;壓載水處理裝置和尾部救生艇拋艇試驗提前至碼頭系泊階段試驗,節省試航時間5個小時。通過系列流程優化,形成固定的試航計劃,單船節約燃油22.5T。
06.加大科技創新提高自動化水平
在項目建造期間,改善小組通過加大科技創新力度,引用自動化設備,不斷提高效率,擴大產能。以推廣使用側吸式自動焊小車,擴大自動焊施工范圍;規劃引進型材下料流水線,提高作業效率;將克令吊筒體焊縫改為自動焊,持續提升自動化生產水平。
在N1087船航行信號燈角度調試交驗上進行科技攻關,使用精控堪畫角度線,在船臺周圍設置永久角度標記,夜間使用望遠鏡進行觀測的方式進行調試交驗。此項改善減少約8小時試航時間,大幅減少試航燃油、帶纜艇、試航人員等相關成本。
同時,還研究自動噴涂機器人、墊塊自動平面掃描系統等技術,系列研究已經取得關鍵突破。
積小流成江海,小成果匯集大改善。63.6k BC項目專項改善委員會將繼續發揮組織作用,持續改善建造工藝,持續提高建造水平,以實際行動打造6.36萬噸系列散貨船精品項目。
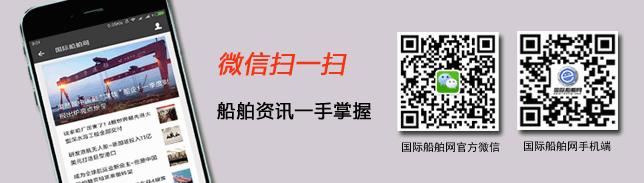